Mexico or China? Discussion Questions 1. Which location provides Polaris the greatest cost advantage? Calculate the NPV of the three locations using a 10% discount rate.
Mexico or China? Discussion Questions 1. Which location provides Polaris the greatest cost advantage? Calculate the NPV of the three locations using a 10% discount rate.
Practical Management Science
6th Edition
ISBN:9781337406659
Author:WINSTON, Wayne L.
Publisher:WINSTON, Wayne L.
Chapter2: Introduction To Spreadsheet Modeling
Section: Chapter Questions
Problem 20P: Julie James is opening a lemonade stand. She believes the fixed cost per week of running the stand...
Related questions
Question
please answer 5 questions below, my deadline is coming in tomorrow
Information are all in 2 pictures

Transcribed Image Text:476
OPERATIONS RESEARCH
Part Seven Case Studies
EXHIBIT 4 Operating metrics by plant location.
Production cost
U.S.
Mexico
China
Capital expenditures, equipment moving costs, and
startup costs (thousands of US$)
U.S.
Mexico
China
Annual demand for Side-by-Sides
Shipping cost from China
Cost per unit
Side-by-Side units per container
Ground transportation cost (US$)
Cost per mile
Side-by-Side units per truck
Other
Tariff for China import
Transportation cost (US$)
Miles to Distribution Center
From Roseau
Tacoma, WA
1,636
2,161
Los Angeles, CA
Irving, TX
1,267
A factory in Mexico would require hiring sixty new
employees, the same as in China. Side-by-Sides would
be shipped to the United States by truck in batches of
26 units at an average cost of $2.30 per mile per batch.
Although trucking companies claimed they could cross
the U.S. border and deliver the products in two days, in
practice it took between two and seven days.
Capital expenditures, equipment moving costs, and
startup costs for a Mexican factory would total $9.5 million.
Under the provisions of NAFTA (North American Free
Trade Agreement), Polaris would pay no tariffs on imports
from Mexico into the United States.
EXHIBIT 5 Demand assumptions.
Annual Demand
(units)
Distribution Center Location
Tacoma, WA
3,650
Los Angeles, CA
7,050
Irving, TX
3,800
Cost per unit
400 USD
4,560 MXN
1,950 CNY
9,500
10,000
14,500 units
5%
190
26
2.30
26
From
Monterrey
2,261
1,505
437
United States
A third option for Polaris's senior management was to
maintain the status quo for production of Side-by-Sides
EXHIBIT 6 Exchange rate history.
CNY/USD
MXN/USD
Year
2000
2001
8.28
9.34
8.28
9.66
2002
8.28
10.80
2003
8.28
11.29
2004
9.19
10.90
2005
7.97
10.90
2006
7.61
10.93
2007
6.95
11.16
2008
6.83
13.50
2009
6.77
12.63
2010
6.65
12.40
CNYChinese yu
MXN - Mexican peso
USD US dollar
EXHIBIT 7 Map of Polaris locations in 2010.
Wyoming MN
product
development
a
o Spirit Lake IA
Roseau MN
manufacturing
Vermillion SD
distribution center
manufacturing)
Monterrey MX
possible plant site
without incurring additional costs. Polaris had tradition-
ally been associated with a strong "Made in America"
Е
culture, and management believed that the company's
employees and customers were proud that all Polaris
products were manufactured in the United States. In
addition, the proximity to headquarters and product
development facilities enabled managers to collaborate
quickly and easily with design engineers and technical
staff in the manufacturing plants.
RECOMMENDING A SOLUTION
As Krishna reviewed the data for each option, he knew
he needed to consider qualitative as well as quantitative
factors to find the best solution for Polaris. Should he
recommend keeping production in the United States, or
should he recommend siting a new plant in either
Mexico or China?
Discussion Questions
1. Which location provides Polaris the greatest cost
advantage? Calculate the NPV of the three locations
using a 10% discount rate.
Polaris Industries Inc.: Global Plant Location
Polaris Industries Inc.: Global Plant Location
Osceola WI
manufacturing
Medina MN
headquarters
477
2. Would your recommendation change if the foreign
exchange rate increased or decreased by 15%?
3. What other factors should be considered in making
this decision?
4. Calculate a weighted scoring model. Decide on
qualitative factors that you think are important in
this decision, e.g. location near R&D, quality, loss
of intellectual property, and currency risk. Then
how much weight you would attach to factors
such as NPV and each of the other factors to total
100%. Then assign a score (1 to 10) to each factor
for each of the three locations. Calculate a total
weighted score by multiplying the weight times.
the factor score and adding over all factors for
each location.
5. Which of the three locations do you recommend and
why?

Transcribed Image Text:474
OPERATIONS RESEARCH
Part Seven Case Studies
EXHIBIT 2 Polaris sales by product.
On-road
vehicles
4%
Snowmobiles
10%
Parts and
accessories
17%
ATVs and
side-by-sides
69%
Polaris was the dominant player in the ORV market
based on market share. In 2010 ORVS accounted for
69 percent of Polaris's sales, with Side-by-Sides com-
prising the majority of sales in this segment. Looking
ahead, the company was excited by the potential
growth in emerging markets. From Latin America to
Asia, Polaris had begun to invest heavily in marketing to
increase awareness of its brand. For example, in China
the company placed off-road image advertising in rac-
ing and extreme sports enthusiast publications. Simi-
larly, in Latin America Polaris was leveraging its brand in
the utility vehicle space to penetrate the substantial
agricultural industries.
MANUFACTURING
In 2010 all of Polaris's manufacturing operations were
located in the northern Midwest. In addition to its corporate
headquarters in Medina, Minnesota, and product develop-
ment and innovation center in Wyoming, Minnesota,
Polaris operated three manufacturing facilities in Roseau,
Minnesota; Osceola, Wisconsin; and Spirit Lake, lowa.
Roseau, the birthplace of the Polaris snowmobile, housed
research, development, and manufacturing for the snow-
mobile, ATV, and Side-by-Side divisions. Roseau also
included a small state-of-the-art injection molding plant
that produced plastic parts for the Roseau and Spirit Lake
factories. As demand grew for ATVs and on-road vehicles,
Polaris established an additional manufacturing facility in
1994 at Spirit Lake. This facility produced select ATV.
watercraft, and Victory motorcycle models. Osceola was
primarily an engine and components supplier for the other
two facilities.
All other components were sourced through more
than 450 global suppliers. In 2010 Polaris sourced
almost 40 percent of its components and materials from
outside the United States, up from 30 percent in 2008.
The company was also increasing low-cost country
(LCC) sourcing, almost doubling its LCC spend to
approximately 24 percent in 2010.
To support its production capabilities in and around
the northern United States, Polaris had three warehouse
facilities in Minnesota for raw materials, export process-
ing, and distribution. When demand for parts, apparel,
and accessories exceeded the company's warehouse
capacity in 1997, a new distribution center was opened
in Vermillion, South Dakota. In addition to its U.S. loca-
tions, Polaris also owned and operated regional sales
and distribution centers in Winnipeg, Canada, and in
Northern Europe and Australia.
REDESIGNING THE SUPPLY CHAIN
Krishna had to consider the tradeoff between manufac-
turing and transportation costs when redesigning the
supply chain for Side-by-Side products. On one hand,
manufacturing in markets with low labor costs could
result in significant savings. Although labor rates in tra-
ditional LCCs such as China were rising. U.S.-based
labor was still more costly. On the other hand, with oil
prices rising steadily, Krishna knew transportation
costs would be far lower if he kept production close
to customers.
Senior management at Polaris was also concerned
about a manufacturing talent gap in the United States.
Over the past twenty years, decreased funding for com-
munity colleges and trade schools had resulted in tech-
nical workers becoming increasingly difficult to find.
Moreover, young trade school graduates were less
interested in moving to the locations where Polaris oper-
ated, which were small towns with only one large
employer. By comparison, well-trained technical talent
was relatively easy to find in many South American and
Asian countries.
Lastly, Polaris expected much of its future sales
growth would come from overseas markets, particularly
emerging markets. There were multiple ways to enter
these markets, including acquisitions and joint ventures,
but building a facility in an emerging market could
potentially help Polaris capture future demand.
CHOOSING A MANUFACTURING LOCATION
Krishna and his team considered several options fort
optimizing the manufacture of Side-by-Sides and the
design of the supply chain. They concluded that the
best options were either to continue production in exist-
ing American factories or to build a new plant in China
or Mexico.
Beyond the specific pluses and minuses of each
location, Krishna needed to consider the following in
making a final decision:
. The majority of demand for Side-by-Sides was in the
southern United States. The states with the highest
share of sales volume in 2010 were Texas and California.
• Side-by-Sides were high volume-to-weight/low value-
to-weight products, which meant that shipping costs
accounted for a large fraction of their retail price.
• Polaris's senior management placed a high value on
ease of communication with its manufacturing plants
and believed that in-person interaction among manag-
ers, design engineers, and production staff was a key
driver of the company's long-term product innovation.
• If Polaris moved production of Side-by-Sides abroad,
the company planned to lay off sixty workers at its
Roseau plant. Each worker would be paid a one-time
severance of $20,000.
. Given the weak economic environment, Polaris as-
sumed that demand for Side-by-Sides would remain
flat for the next five years.
Data on labor costs, production costs, transportation
costs, capital expenditures, and exchange rates for each
location are included in Exhibit 3 through Exhibit 6.
China
Polaris's senior executives were excited about the low
costs in China, but labor costs had been rising in the
manufacturing-heavy eastern region; over time the com-
pany would likely have to look further inland to find low-
cost labor, which would further increase the length and
variability of product transportation. Polaris also had
EXHIBIT 3 Labor assumptions.
Monthly Wages
1999
2000
2001
2002
2003
2004
2005
2006
2007
2008
Hourly wage
Working months/year
United States
China (CNY)
649.5
729.2
814.5
916.8
1,041.3
1,169.4
1,313.1
1,497.2
1,740.3
2,016.0
$26/hour
12
Polaris Industries Inc.: Global Plant Location
Polaris Industries Inc.: Global Plant Location
concerns about its ability to successfully collaborate
with a Chinese factory due to time-zone differences and
cultural dissimilarities.
Operating a factory in China would require Polaris to
hire sixty new employees on location. It also would
result in a one-time charge of $10 million for capital
expenditures, equipment moving costs, and startup
costs. Polaris would have to pay a 5 percent tariff on all
production and transportation costs when importing
products into the United States.
Side-by-Sides made in China would be transported
to the United States on container vessels, with each
container holding twenty-six vehicles. The cost to ship
one vehicle to the United States from China was $190
per unit, or $4,940 per container. Although shipping
companies claimed the containers would reach the
United States in about twenty days, in practice shipping
time was highly variable, with a range of nineteen to
thirty-three days.
Mexico
Polaris's senior management saw several qualitative
advantages to operating a foreign manufacturing facility
in Monterrey, Mexico. (See Exhibit 7 for map.) Monterrey
was relatively close to the United States, which would
allow for easier in-person collaboration between the
manufacturing facility and Polaris's staff. In addition to
geographical proximity, managers believed cultural
familiarity would make collaborating with a Mexican
workforce easy. Lastly, although Polaris believed that
long-term sales growth would come from emerging mar-
kets in Asia, it also believed that near-term growth would
occur in the United States-particularly in the southern
United States, an area close to Monterrey.
Annual Wage Growth (%)
Mexico (MXN)
2,392.0
2,910.5
3,367.6
3,537.5
3,737.7
3,858.8
3,983.8
4,112.9
4,246.2
4,383.7
China (CNY)
12
12
13
14
12
12
14
16
16
Mexico (MXN)
22
16
wwwwwar555
3
475
3
Expert Solution

This question has been solved!
Explore an expertly crafted, step-by-step solution for a thorough understanding of key concepts.
This is a popular solution!
Trending now
This is a popular solution!
Step by step
Solved in 2 steps with 3 images

Recommended textbooks for you
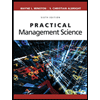
Practical Management Science
Operations Management
ISBN:
9781337406659
Author:
WINSTON, Wayne L.
Publisher:
Cengage,
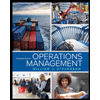
Operations Management
Operations Management
ISBN:
9781259667473
Author:
William J Stevenson
Publisher:
McGraw-Hill Education
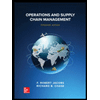
Operations and Supply Chain Management (Mcgraw-hi…
Operations Management
ISBN:
9781259666100
Author:
F. Robert Jacobs, Richard B Chase
Publisher:
McGraw-Hill Education
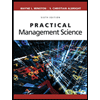
Practical Management Science
Operations Management
ISBN:
9781337406659
Author:
WINSTON, Wayne L.
Publisher:
Cengage,
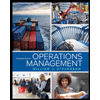
Operations Management
Operations Management
ISBN:
9781259667473
Author:
William J Stevenson
Publisher:
McGraw-Hill Education
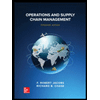
Operations and Supply Chain Management (Mcgraw-hi…
Operations Management
ISBN:
9781259666100
Author:
F. Robert Jacobs, Richard B Chase
Publisher:
McGraw-Hill Education
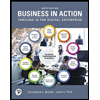
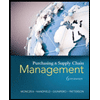
Purchasing and Supply Chain Management
Operations Management
ISBN:
9781285869681
Author:
Robert M. Monczka, Robert B. Handfield, Larry C. Giunipero, James L. Patterson
Publisher:
Cengage Learning
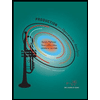
Production and Operations Analysis, Seventh Editi…
Operations Management
ISBN:
9781478623069
Author:
Steven Nahmias, Tava Lennon Olsen
Publisher:
Waveland Press, Inc.