Activity-based product costing Sweet Sugar Company manufactures three products (white sugar, brown sugar, and powdered sugar) in a continuous production process. Senior management has asked the controller to conduct an activity-based costing study. The controller identified the amount of factory overhead required by the critical activities of the organization as follows: Activity Production Setup Inspection Shipping Customer Service Total Budgeted Activity Cost $435,000 237,000 107,800 122,100 80,400 $982,300 The activity bases identified for each activity are as follows: Activity Activity Base Production Machine hours Setup Number of setups Inspection Number of inspections Shipping Number of customer orders Customer Service Number of customer service requests The activity-base usage quantities and units produced for the three products were determined from corporate records and are as follows: Machine Hours Number of Setups Number of Inspections Number of Customer Customer Service Orders Requests Units White sugar 3,300 150 280 740 60 8,250 Brown sugar 2,100 230 420 2,040 380 5,250 Powdered sugar 2,100 220 700 920 160 5,250 Total 7,500 600 1,400 3,700 600 18,750 Each product requires 0.9 machine hour per unit. Required: If required, round all per unit amounts to the nearest cent. 1. Determine the activity rate for each activity. Production Setup Inspection Shipping per machine hour per setup per inspection hour Customer service per cust. ord. per customer service request 2. Determine the total and per-unit activity cost for all three products. White sugar Brown sugar Total Activity Cost Activity Cost Per Unit Powdered sugar 3. Why aren't the activity unit costs equal across all three products since they require the same machine time per unit? The unit costs are different because the products consume many activities in ratios different from the
Process Costing
Process costing is a sort of operation costing which is employed to determine the value of a product at each process or stage of producing process, applicable where goods produced from a series of continuous operations or procedure.
Job Costing
Job costing is adhesive costs of each and every job involved in the production processes. It is an accounting measure. It is a method which determines the cost of specific jobs, which are performed according to the consumer’s specifications. Job costing is possible only in businesses where the production is done as per the customer’s requirement. For example, some customers order to manufacture furniture as per their needs.
ABC Costing
Cost Accounting is a form of managerial accounting that helps the company in assessing the total variable cost so as to compute the cost of production. Cost accounting is generally used by the management so as to ensure better decision-making. In comparison to financial accounting, cost accounting has to follow a set standard ad can be used flexibly by the management as per their needs. The types of Cost Accounting include – Lean Accounting, Standard Costing, Marginal Costing and Activity Based Costing.


Step by step
Solved in 5 steps

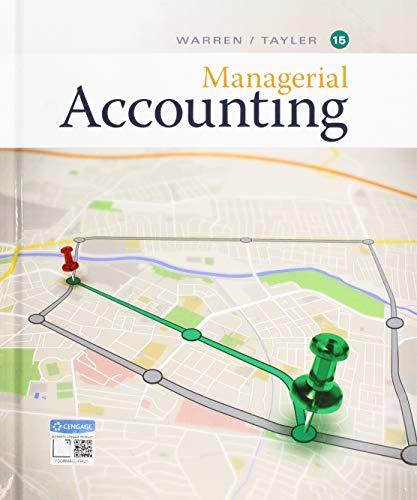
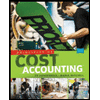
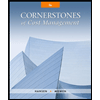
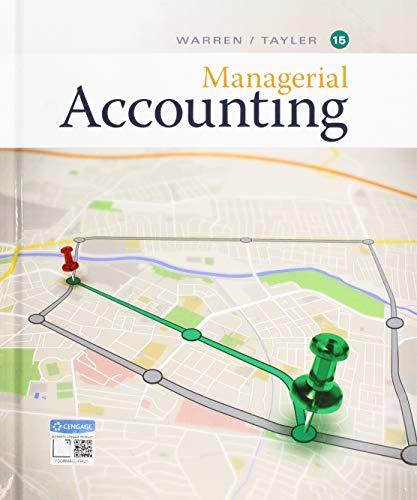
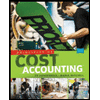
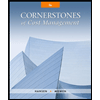
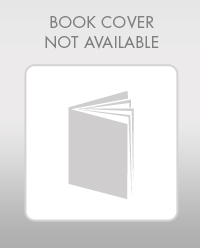
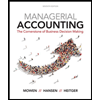