Consider a brake testing bench as shown in the figure. Motor 16.1 50 20 Clutch + X A motor speeds up the system through the use of a clutch. Electric control is used to maintain motor speed (constant motor speed). The clutch is actuated from the motor side by a force P equal to 5000 N. A flywheel weighing 60 kg is used to provide inertia to the system. The motor speed is 950 RPM. 250 The next figure shows a proposed shaft onto which the brake side clutch plate, flywheel, and brake disc will be placed. The shaft will be machined from AISI 1050 CD steel, Sut= 690 MPa; Sy=580 MPa. 1251 25.4 Flywheel 200 Brake (Callipers) 50 X 20 Brake (Disc) Units in [mm] Bearing End milled keyway for flywheel placement For the proposed shaft determine the fatigue factor of safety for infinite life using the modified Goodman criteria only at point 1 (the end-milled keyseat where the flywheel will be placed). Do this for two scenarie a) While the clutch is engaged, and slippage occurs. b) While the clutch is engaged, and no slippage occurs (the brake side is rotating at the same speec the motor side). Assume the following: • The brake remains disengaged. Neglect the weight of the shafts, clutch, and brake disc. Neglect friction effects at the bearings. Keyseats are end milled. Use first iteration estimates for stress concentrations. The theoretical stress-concentration factor for axial loading at the keyseat is K₂ = 3.0. A reliability of 99% is required. See clutch properties and relevant tables on next page.
Consider a brake testing bench as shown in the figure. Motor 16.1 50 20 Clutch + X A motor speeds up the system through the use of a clutch. Electric control is used to maintain motor speed (constant motor speed). The clutch is actuated from the motor side by a force P equal to 5000 N. A flywheel weighing 60 kg is used to provide inertia to the system. The motor speed is 950 RPM. 250 The next figure shows a proposed shaft onto which the brake side clutch plate, flywheel, and brake disc will be placed. The shaft will be machined from AISI 1050 CD steel, Sut= 690 MPa; Sy=580 MPa. 1251 25.4 Flywheel 200 Brake (Callipers) 50 X 20 Brake (Disc) Units in [mm] Bearing End milled keyway for flywheel placement For the proposed shaft determine the fatigue factor of safety for infinite life using the modified Goodman criteria only at point 1 (the end-milled keyseat where the flywheel will be placed). Do this for two scenarie a) While the clutch is engaged, and slippage occurs. b) While the clutch is engaged, and no slippage occurs (the brake side is rotating at the same speec the motor side). Assume the following: • The brake remains disengaged. Neglect the weight of the shafts, clutch, and brake disc. Neglect friction effects at the bearings. Keyseats are end milled. Use first iteration estimates for stress concentrations. The theoretical stress-concentration factor for axial loading at the keyseat is K₂ = 3.0. A reliability of 99% is required. See clutch properties and relevant tables on next page.
Automotive Technology: A Systems Approach (MindTap Course List)
6th Edition
ISBN:9781133612315
Author:Jack Erjavec, Rob Thompson
Publisher:Jack Erjavec, Rob Thompson
Chapter44: Four- And All-wheel Drive
Section: Chapter Questions
Problem 4RQ: Briefly explain how a Haldex clutch works.
Related questions
Question
can you solve this please, this is not graded, simply an example
![Consider a brake testing bench as shown in the figure.
Motor
A motor speeds up the system through the use of a clutch. Electric control is used to maintain motor speed
(constant motor speed). The clutch is actuated from the motor side by a force P equal to 5000 N. A flywheel
weighing 60 kg is used to provide inertia to the system. The motor speed is 950 RPM.
25
The next figure shows a proposed shaft onto which the brake side clutch plate, flywheel, and brake disc will
be placed. The shaft will be machined from AISI 1050 CD steel, Sut= 690 MPa; Sy = 580 MPa.
16.1
50
20
Flywheel
Clutch
Brake (Callipers)
+
X
250
25.4
200
50
Brake (Disc)
20
The brake remains disengaged.
Neglect the weight of the shafts, clutch, and brake disc.
Neglect friction effects at the bearings.
Units in [mm]
Bearing
End milled keyway for
flywheel placement
For the proposed shaft determine the fatigue factor of safety for infinite life using the modified Goodman
criteria only at point 1 (the end-milled keyseat where the flywheel will be placed). Do this for two scenarios:
a) While the clutch is engaged, and slippage occurs.
b) While the clutch is engaged, and no slippage occurs (the brake side is rotating at the same speed as
the motor side).
Assume the following:
Keyseats are end milled. Use first iteration estimates for stress concentrations.
The theoretical stress-concentration factor for axial loading at the keyseat is K₂ = 3.0.
A reliability of 99% is required.
See clutch properties and relevant tables on next page.](/v2/_next/image?url=https%3A%2F%2Fcontent.bartleby.com%2Fqna-images%2Fquestion%2Fa36211ff-413d-45db-8330-03ac493e19cc%2Faaa00a13-cbac-42f3-baf2-f39f8948416e%2Fgrkr2wo_processed.png&w=3840&q=75)
Transcribed Image Text:Consider a brake testing bench as shown in the figure.
Motor
A motor speeds up the system through the use of a clutch. Electric control is used to maintain motor speed
(constant motor speed). The clutch is actuated from the motor side by a force P equal to 5000 N. A flywheel
weighing 60 kg is used to provide inertia to the system. The motor speed is 950 RPM.
25
The next figure shows a proposed shaft onto which the brake side clutch plate, flywheel, and brake disc will
be placed. The shaft will be machined from AISI 1050 CD steel, Sut= 690 MPa; Sy = 580 MPa.
16.1
50
20
Flywheel
Clutch
Brake (Callipers)
+
X
250
25.4
200
50
Brake (Disc)
20
The brake remains disengaged.
Neglect the weight of the shafts, clutch, and brake disc.
Neglect friction effects at the bearings.
Units in [mm]
Bearing
End milled keyway for
flywheel placement
For the proposed shaft determine the fatigue factor of safety for infinite life using the modified Goodman
criteria only at point 1 (the end-milled keyseat where the flywheel will be placed). Do this for two scenarios:
a) While the clutch is engaged, and slippage occurs.
b) While the clutch is engaged, and no slippage occurs (the brake side is rotating at the same speed as
the motor side).
Assume the following:
Keyseats are end milled. Use first iteration estimates for stress concentrations.
The theoretical stress-concentration factor for axial loading at the keyseat is K₂ = 3.0.
A reliability of 99% is required.
See clutch properties and relevant tables on next page.

Transcribed Image Text:An axial flat disc clutch with the following properties is used:
Bending or axial:
Va=0.246-3.08 (10³) Su+1.51 (105) S
-2.67 (108) s 50 Sut ≤ 250 kpsi
Va=1.24-2.25 (10³) St+1.60 (106)S-4.11 (10-10)5 340 ≤ Sut ≤1700 MPa
Torsion:
Va=0.190-2.51 (10³)S +1.35 (105)S-2.67 (108)s
Va=0.958-1.83 (10³) Sur +1.43 (106) S-4.11 (10-10)
Table 6-2
Inner diameter = 50 mm
Outer diameter = 100 mm
Coefficient of friction = 0.4
Friction contact surfaces or pairs = 1
Uniform wear is considered
Surface Finish
Ground
Curve Fit Parameters for Surface Factor, Equation
(6-18)
Machined or cold-drawn
Hot-rolled
As-forged
Factor a
Sut, kpsi Sut, MPa
1.38
1.21
2.00
11.0
12.7
3.04
38.6
50 Sur 220 kpsi
340 ≤Sat ≤ 1500 MPa
54.9
Exponent b
-0.067
-0.217
-0.650
-0.758
(6-35)
(6-36)
Expert Solution

This question has been solved!
Explore an expertly crafted, step-by-step solution for a thorough understanding of key concepts.
Step by step
Solved in 4 steps with 13 images

Knowledge Booster
Learn more about
Need a deep-dive on the concept behind this application? Look no further. Learn more about this topic, mechanical-engineering and related others by exploring similar questions and additional content below.Recommended textbooks for you
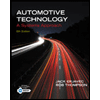
Automotive Technology: A Systems Approach (MindTa…
Mechanical Engineering
ISBN:
9781133612315
Author:
Jack Erjavec, Rob Thompson
Publisher:
Cengage Learning
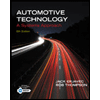
Automotive Technology: A Systems Approach (MindTa…
Mechanical Engineering
ISBN:
9781133612315
Author:
Jack Erjavec, Rob Thompson
Publisher:
Cengage Learning