Project 2 GSCM 450
.docx
keyboard_arrow_up
School
Liberty University *
*We aren’t endorsed by this school
Course
3142
Subject
Business
Date
May 4, 2024
Type
docx
Pages
22
Uploaded by ChancellorRamPerson95 on coursehero.com
Project 2: Drop ‘Till You Shop
Yatnary Villanueva, Joanna Nghiem, Alex Casillas, Ana Nunez, Hamed Al Balushi Team 2
Portland State University
Project 2: Drop ‘Till You Shop
Yatnary Villanueva, Joanna Nghiem, Alex Casillas, Ana Nunez, Hamed Al Balushi GSCM 450 - Winter 2024
Scope Management Plan Operational Overview: The warehouse will function as a central facility for receiving, storing, and shipping our top dropshipping items to maintain our current lead time with our customers. It will prioritize efficiency, accuracy, and timely processing of orders. The operations of this warehouse will be conducted as follows:
Number of Docks: For our new warehouse, we will be using the following number of docks for our operations: Inbound Shipments: Two docks designated for receiving goods from suppliers. Outbound Shipments: Two docks for loading trucks and dispatching orders to customers.
Storage Method: Products will be stored using pallet racking systems and bin locations to maximize space and accessibility. All inventory will be categorized using the ABC method, and thus, high-demand items will be strategically placed closer to the shipping area for quick retrieval. Though stored items are our top dropshipping items, an ABC classification will be necessary to optimize inventory.
Product Movement: Product movement will be facilitated using pallet jacks and forklifts for efficient transportation within the warehouse. Barcode scanning systems will track product movement from receiving to storage to outbound shipments, ensuring accuracy and visibility. Proper providers for receiving and shipping items will ensure consistency and accuracy with the warehouse employees. Cycle counts will be conducted daily for inventory accuracy on all items and transferred to our warehouse management system.
Technology Integration: RFID technology will be implemented for real-time inventory tracking and management, enhancing accuracy and efficiency. A Warehouse Management System (WMS) software will be utilized to optimize operations, monitor inventory levels, and streamline
order fulfillment processes. All required employees will be trained on the WMS, and we will keep all SOPs on file. Ownership of Trucks: The warehouse will work with a third-party delivery company to save on costs such as labor, vehicle maintenance, registration of vehicles, gas, etc. These carriers will also engage in long-distance shipments. Shifts and Workforce: The warehouse will operate on a three-shift schedule, enabling round-the-
clock operations to meet customer demands and optimize productivity. Each shift will be staffed with trained personnel, including supervisors, forklift operators, order pickers, packers, and quality control inspectors, ensuring smooth operations and order accuracy. Annual Revenue: Our company’s annual revenue is $100 Million.
3/6/2024
Page 2
Yatnary Villanueva, Joanna Nghiem, Alex Casillas, Ana Nunez, Hamed Al Balushi GSCM 450 - Winter 2024
Net Income:
Our company’s net income is $18,750,000.
Operating Costs:
$6,250,000
Return on Investment:
86% Location: We recommend that the company build its storage warehouse in Savannah, Georgia. After doing research, we found that Georgia has a well-developed transportation infrastructure, low operating
costs, highly skilled workers, excellent accessibility to the market, and a business-friendly environment (Georgia Power, p.1). Further, according to Georgia Power, there are also 5,000 + miles of rail through Georgia, 9,500 daily transactions at GA ports, and 900 M sq. ft of warehouse space in GA. When it comes to the workforce, Georgia has a total of 346,000,000 warehouse-related jobs, a projected +9% growth from 2021-2031 in warehouse jobs, with a minimum wage of $7.25 and a medium wage of $16.37. The cost-related benefits of establishing a warehouse distribution location in Georgia include but are not limited to a low state corporate tax rate of 5.75%, low overall cost of doing business, competitive wage rates with low unionization, and tax exemptions on warehouse inventory (Georgia Power). Business conditions that are driving this project:
There has been a seven-day increase in our lead time, which poses a threat to decreasing customer satisfaction. Therefore, there is a need to explore options to get it back to our promised number of fourteen days. We estimate that we will hit ROI within five years as our year-over-year growth has steadily increased by 35% every year. When it comes to our market share, similarly to our year-over-year growth, it has continued to steadily increase, with Drop ‘Till You Drop currently holding 23% of the market share. What is the warehouse going to be used for? Storing, cross-docking? The warehouse will be used as a storage facility. What product are you storing? The specific product that we plan on storing is our top-selling furniture pieces. This includes chairs, tables, bed frames, etc.
Business needs a description of the project from a high view: CEO, As our company continues to thrive and meet customer demands, it has become imperative to address the recent challenge posed by our supplier’s increased lead time to 21 days. This adjustment has the potential to impact our ability to maintain our current 14-day lead time to customers, which is a key differentiator in the market. To counteract this, I propose the 3/6/2024
Page 3
Yatnary Villanueva, Joanna Nghiem, Alex Casillas, Ana Nunez, Hamed Al Balushi GSCM 450 - Winter 2024
construction of a 100,000 sqft warehouse dedicated to storing our top-selling items. This strategic move will not only safeguard our commitment to customers but also position us as a reliable and efficient supplier in the face of industry uncertainties.
The construction of this warehouse is not merely a response to a short-term issue but a strategic investment in the long-term sustainability and growth of our business. By having a facility dedicated to our best-selling products, we can ensure that we always have sufficient inventory on
hand to meet customer demands within our committed 14-day lead time. This not only preserves our reputation for reliability but also demonstrates our commitment to customer satisfaction, a cornerstone of our brand identity.
In addition to safeguarding our lead time commitments, the warehouse can be designed to accommodate future growth. With modular storage solutions and scalability in mind, we can adapt to changing market dynamics and increased product demand. This flexibility positions us to navigate uncertainties in the supply chain landscape effectively and maintain a competitive edge.
Furthermore, the warehouse provides us with the opportunity to implement cutting-edge technologies and automation in inventory management. Advanced logistics systems can optimize
order fulfillment processes, minimizing the time it takes to pick, pack, and ship products. This operational efficiency not only supports our commitment to timely deliveries but also contributes
to overall cost savings, investing in the warehouse is a financially sound decision.
The construction of a 100,000 sqft warehouse represents a strategic imperative for our company. It not only addresses the immediate challenge posed by the supplier’s extended lead time but also
sets the stage for enhanced operational efficiency, cost savings, and future growth.
Success Criteria and who buys off at end: “The customer has a fully functioning and operationally complete facility that meets all local building codes”.
Project Milestone Schedule (12-Month Timeline)
Table 1: Milestones Milestone
Start date
End date
Secure funds and location of warehouse January 1st, 2024
January 31st, 2024
Design a warehouse layout and flow
February 1, 2024
February 28, 2024
Get project approval and permits necessary April 1, 2024
May 1, 2024
3/6/2024
Page 4
Yatnary Villanueva, Joanna Nghiem, Alex Casillas, Ana Nunez, Hamed Al Balushi GSCM 450 - Winter 2024
Site preparation and excavation. Determine the depth of foundation and concrete pouring.
June 1, 2024
June 31, 2024
Framing, structural, roofing, and exterior work
July 1, 2024
August 1, 2024
Electrical, plumbing, fire protection, and alarm systems
August 10, 2024
September 10, 2024
Drywall, interior, flooring, and light fixtures
September 12, 2024
October 12, 2024
Landscaping
October 15, 2024
November 15, 2024
Final inspection and occupancy November 17, 2024
December 17, 2024
Move-in coordination and facility setup
December 17, 2024
December 31, 2024
The milestones above are sequenced steps required to execute a warehouse project. It is essential to include a schedule for preparing, developing, evaluating, and reporting the project's execution.
In order to have a successful project, milestones are important and must be on schedule. Key Stakeholders
Table 2: Key Stakeholders
Stakeholder Role
Key Stakeholder
Responsibilities
Chief Executive Officer (CEO)
Endorses and drives strategic initiatives
The CEO is responsible for providing the overall strategic
direction and vision for the company. In this project, the CEO's role involves endorsing the initiative and ensuring its alignment with the company's long-term goals.
Chief Operations Officer (COO)
Oversees logistical and operational aspects of the warehouse, ensuring integration with existing processes
The COO is tasked with overseeing the day-to-day operations of the warehouse. This includes managing logistics, optimizing operational processes, and ensuring seamless integration 3/6/2024
Page 5
Yatnary Villanueva, Joanna Nghiem, Alex Casillas, Ana Nunez, Hamed Al Balushi GSCM 450 - Winter 2024
and communication with the company's existing supply chain and manufacturing operations.
Chief Financial Officer (CFO)
Analyze financial feasibility and assesses long-term sustainability of the investment
The CFO assesses the financial viability of the warehouse construction. This involves conducting a cost-
benefit analysis, evaluating return on investment, and ensuring the long-term financial sustainability of the project.
Supply Chain Manager
Manages the flow of inventory and optimizes warehouse processes
The Supply Chain Manager is
responsible for the efficient flow of inventory within the warehouse. This includes inventory management, demand forecasting, and implementing strategies to optimize warehouse processes
for increased efficiency and productivity.
Head of Customer Relations
Maintains commitment to customer satisfaction, which is crucial for preserving the company's reputation for timely deliveries
The Head of Customer Relations is essential for ensuring that the warehouse project aligns with the company's commitment to customer satisfaction, which is similar to a feedback process. This involves maintaining communication with customers and addressing any concerns related to order fulfillment and delivery timelines.
Customers (Consumers)
Buys the product, their Customers are important 3/6/2024
Page 6
Your preview ends here
Eager to read complete document? Join bartleby learn and gain access to the full version
- Access to all documents
- Unlimited textbook solutions
- 24/7 expert homework help
Related Questions
Scenario
Capstone project
Goal Statement: Our goal is to improve the overall mental health status of veterans of the Canadian Armed Forces and RCMP by up to 80% for those struggling with mental health challenges by facilitating real-time accessibility to a peer support platform utilizing a mobile app to fill the gap that currently exists when veterans are awaiting appointments for psychological supports that are currently funded by Veterans Affairs of Canada. We aim to reduce the strain on the general health system due to the repeated appointments with a veteran's primary care practitioner to inquire about further mental health resources and to improve a veterans quality of life while they are adjusting to civilian life in between their federally funded psychological supports.
Please answer in detail
1 communication strategy for the above project
2. Pilot or stakeholder feedback outcomes
3. Recommendation for next steps
arrow_forward
Scenario 8.3- Mousetraps
A company faces the aggregate planning problem shown in the table below. Cost of regular
production is $15 per unit, the cost of producing the same unit on overtime is $22.50, the cost
subcontracting is $27 per unit, and the cost of carrying a unit in inventory from one month to the next
is $10.
Forecast
Beginning Inventory
Regular Time
Overtime
Subcontracting
Ending Inventory
The labor contract at the plant prohibits both overtime and subcontracting output to exceed 250
units in any five-month window. The plant capacity is 20 units per day produced using two shifts and
the plant runs seven days a week. By policy, management wants to avoid stockouts.
August
Which month has a positive ending inventory for the optimal aggregate plan for Scenario 8.3?
September
July
800
140
O October
August September October November
650 450
550
900
November
arrow_forward
Answer Activity 3
arrow_forward
DEFINE Critical path analysis
arrow_forward
For the following schedule, draw the arrow and node
diagram.
Activity Duration IPA
A----3----
ABCDEFGHISKENN
с
H----------5------
--4-
-3---
L-
-6----
-3------
-9------
-1-
M
N-----
3636
B
A
-9
--A
B
C, D
C,D
E
F, G, H
F, G, H
I
J, K
- GOD BLESS ---
arrow_forward
Describe the role of supply chain management in project management and its significance in guaranteeing the successful completion of the project.
arrow_forward
Preceding
Activity
Crashed Cost per
week
$600
$700
$400
Activity
Normal Completion
Time (week)
Crashed Completion
time (week)
A
7
5
B
12
10
A
8
2
$800
$300
$500
E
C, D
5
4
F
E
9
8
D. F
10
10
i.
Draw the network diagram linking all the activities in a way that it shows if there exist any
preceding activity/activities before starting each of the mentioned activities in the above
table,
ii.
Showing the earliest start time, the earliest finish time, the latest start time and the latest
finish time of each of the activities in the project determine the completion time of the
project and the critical path.
ii.
Find the slack time (delay time) of each of the activities, the critical and the non-critical
activities.
Find the minimum possible completion time of the project by considering the crashed
completion times and the minimal total cost of that crashing the project.
iv.
Need proper handwritten answers. Thank you!
arrow_forward
The Custom Bike Company has set up a weighted scoring matrix for evaluation of potential projects. Following are five projects under consideration. Criteria Strong sponsor Supports business strategy Urgency 10% of sales from new products Competition Fill market gap Weight 2 4 2 5 1 2 Project 1 6 8 9 5 4 0 Project 2 9 8 4 2 7 10 Project 3 3 2 3 9 4 8 Project 4 9 6 6 1 4 0 Project 5 6 0 7 4 1 0 Using the scoring matrix above, what score would you give to each project?
arrow_forward
Case stady:
Global Village: A tourist attraction
Global Village is the region’s leading family outdoor cultural and entertainment destination and one of Dubai’s most exciting and unique annual tourism and cultural destination. The theme park offers a vast selection of multicultural entertainment and retail options.
Launched in 1997, Global Village made its entrance on the Creek Side opposite Dubai Municipality, and later moved to Oud Metha and then Dubai Festival City, until it found a permanent home on the outskirts of Dubai Land in 2005. Over the past 17 years, Global Village has been providing cultural entertainment along with an international shopping experience to millions of visitors.
From hosting 18 country pavilions in 1997, Global Village has expanded over the years to now include over 37 pavilions, with added entertainment and culinary attractions with every season. Apart from this breathtaking live performances, mouth-watering cuisine, authentic handicrafts and merchandise…
arrow_forward
Describe Short Term High Priority Objectives.
arrow_forward
Carlos Cavalas, the manager of Echo Products’ Brazilian Division, is trying to set the production schedule for the last quarter of the year. The Brazilian Division had planned to sell 70,070 units during the year, but by September 30 only the following activity had been reported:
Units
Inventory, January 1
0
Production
71,100
Sales
63,700
Inventory, September 30
7,400
The division can rent warehouse space to store up to 30,500 units. The minimum inventory level that the division should carry is 2,800 units. Mr. Cavalas is aware that production must be at least 4,440 units per quarter in order to retain a nucleus of key employees. Maximum production capacity is 44,200 units per quarter.
Demand has been soft, and the sales forecast for the last quarter is only 19,500 units. Due to the nature of the division’s operations, fixed manufacturing overhead is a major element of product cost.
Required:
1a. Assume that the division is using variable costing. How many…
arrow_forward
Roger Ginde is developing a program in supply chain management certification for managers. Ginde has listed a number of activities that must be completed before a training program of this nature
could be conducted. The activities, immediate predecessors, and times appear in the accompanying table:
Immediate Predecessor(s)
Activity
ABCDEFG
This exercise contains only parts b, c, and d.
b) The critical activities for the leadership training program development project are
B
A, D
C
E, F
Time (days)
4
5
3
10
4
6
10
arrow_forward
Nikos Anastopoulos of EMPROSS Strategic IT Consultants, leads the development of a new football stadium. He developed the activities, durations, and predecessor relationships in the following table for delivering company valuations.
Activity
Predecessor
Duration in Weeks
A
-
5
B
-
3
C
A, B
8
D
C
3
E
-
4
F
E
10
G
F
8
H
E
18
I
D
20
J
D, G, I
7
K
I
5
L
H
10
6A. Draw the Network Diagram, and identify and discuss the project duration and the critical path using the following activity notation:
the first pic:
First: Draw the precedence diagram.
Second: Using the notation given identify the duration of the project: you can type it.
Third: identify the critical part and explain the critical path.
Fourth: Explain your answer. This can be done by describing the process and the observations done once the answer has been found.
6B. Draw the project’s Gantt chart
First: The…
arrow_forward
Alif Aziz holds the position of Project Executive at Disloyal Corporation Berhad, with a basic salary of RM3,400.00. Due to his regular client meetings, the company provides him with fixed monthly allowances of RM200.00 for a handphone and RM400.00 for petrol. Additionally, Alif Aziz occasionally works extra hours, including on his rest days and public holidays. Last month (March 2024), he worked extra hours as detailed below:
Working extra hours from 6.00pm to 9.00pm, from Monday to Friday (5 days in total).
Working on Sunday (3rd and 10th March) from 1.00pm to 5.00pm.
Working on Sunday (1 7th and 24th March) from 5.30pm to 10.30pm. Working on public holiday from 8.30am to 9.30pm (1 day).
Given that Disloyal Corporation working hours are as below:
Monday to Friday
8.30am - 5.30pm
Saturday
8.30am — 1.30pm
Sunday / Public Holiday
Close
I . What is Alif Aziz' daily wage rate? (Round your answer into two decimal points)
A. RM154.28 per day
B.…
arrow_forward
Alif Aziz holds the position of Project Executive at Disloyal Corporation Berhad, with a basic salary of RM3,400.00. Due to his regular client meetings, the company provides him with fixed monthly allowances of RM200.00 for a handphone and RM400.00 for petrol. Additionally, Alif Aziz occasionally works extra hours, including on his rest days and public holidays. Last month (March 2024), he worked extra hours as detailed below:
Working extra hours from 6.00pm to 9.00pm, from Monday to Friday (5 days in total).
Working on Sunday (3rd and 10th March) from 1.00pm to 5.00pm.
Working on Sunday (1 7th and 24th March) from 5.30pm to 10.30pm. Working on public holiday from 8.30am to 9.30pm (1 day).
Given that Disloyal Corporation working hours are as below:
Monday to Friday
8.30am - 5.30pm
Saturday
8.30am — 1.30pm
Sunday / Public Holiday
Close
6. What is the total amount Alif Aziz earned for working from 5.30pm to 10.30pm on 17th and 24th March? (Round your…
arrow_forward
Why is it important to conduct transportation project evaluation using life-cycle cost analysis approach?
arrow_forward
Describe Long Term High Priority Objectives.
arrow_forward
Tools
View
Week 3 Bonus Activity-
DEMAND FORECASTING CASE STUDY
After reviewing the forecasting demonstration and
looking over the slides, complete the following case
activity and transfer your answers to the appropriate
questions in the Canvas activity quiz.
You have been hired as a demand planning intern for
Hawaiian Island Creations (HIC). They want you to de-
velop a forecast for their HIC Papanui style of sun-
glasses. The goal is to determine how many pair they
will produce to meet retailer demand in July 2021. During
your first meeting, you were handed some data to work
with and the product team talked about the company's
upcoming promotional blitz to support Summer Break '21
in major vacation destinations.
Month
Forecast
Demand
January 2021
4.000
3,300
February 2021
4,200
3,900
March 2021
4,500
4,300
April 2021
4.800
4,200
May 2021
5 000
5.400
of 4
P Type here to search
立
arrow_forward
K
Roger Ginde is developing a program in supply chain management certification for managers. Ginde has listed a
number of activities that must be completed before a training program of this nature could be conducted. The activities,
immediate predecessors, and times appear in the accompanying table:
Activity Immediate Predecessor(s)
ABCDEFG
B
A, D
C
E, F
Time (days)
2
7
2
10
4
5
8
This exercise contains only parts b, c, and d.
b) The critical activities for the leadership training program development project are B-D-E-G
c) The project length for the leadership training program development project =
days.
arrow_forward
Roger Ginde is developing a program in supply chain management certification for managers. Ginde has listed a num- ber of activities that must be completed before a training program of this nature could be conducted. The activities, immediate pre-decessors, and times appear in the accompanying table: A—2 B—5 C—1 D B 10 E A, D 3 FC6 G E, F 8
A) Develop an AON network for this problem.b) What is the critical path?c) What is the total project completion time?
Please answer A B C and show work
arrow_forward
hari
Salman bin abdulaziz University, Al Kharj
College of Business Administration
Management Department
Management Science (MGT321)
Name:
University No.:
Assignment 1
Exercisel
(a):
What do you mean by Linear Programming Problem? Write the general form of an LPP.
(b):
Cycle Trends is introducing two new lightweight bicycle frames, the Deluxe and the Professional,
to be made from aluminum and steel alloys. The anticipated unit profits are SAR 30 for the
Deluxe and SAR 35 for the Professional.
The number of pounds of each alloy needed per frame is summarized in the following table. A
supplier delivers 90 pounds of the aluminum alloy and 100 pounds of the steel alloy weekly.
How many Deluxe and Professional frames should Cycle Trends produce each week?
Table: Pounds of each alloy needed per frame
Frame
Aluminum Alloy
Steel Alloy
Deluxe
4
3
Professional
3
Formulate the above problem as linear programming problem.
Exercise2:
4
arrow_forward
The Stone River Textile Mill was inspected by OSHA and found to be in violation of a number of safety regulations. The OSHA inspectors ordered the mill to alter some existing machinery to make it safer (add safety guards, etc.); purchase some new machinery to replace older, dangerous machinery; and relocate some machinery to make safer passages and unobstructed entrances and exits. OSHA gave the mill only 35 weeks to make the changes; if the changes were not made by then, the mill would be fined $300,000. The mill determined the activities in a CPM/PERT network that would have to be completed and then estimated the indicated activity times, as shown in the following table: Construct the project network for this project and determine the following: a. Expected activity times b. Earliest and latest activity times and activity slack c. Critical path d. Expected project duration and variance e. The probability that the mill will be fined $300,000
arrow_forward
SAQ 3: For the present, construct the appropriate network diagram
representing this data. Include "Start" and "End" activities as appropriate.
Activity
Duration
Preceding Activity
Start
A
5
4
C
6
A
E
5
B
F
6.
С, D
End
Е, F
2.
arrow_forward
Describe the differences between Gantt charting, FCS, and the theory of constraints.
arrow_forward
Please answer b and c activity’s a-k
arrow_forward
Week
1
2
3
4
5
6
7
8
9
10
Task 1
32
58
53
14
Task 2
21
65
95
43
Task 3
92
Task 4
a. What is the cumulative actual cost at the end of week 6?
b. Is there a cost overrun or underrun at the end of week 6? What is the amount?
arrow_forward
Case Study
Contract logistics is a growth market. Dachser Far East Ltd is a leading logistics operator. A definition of contract logistics is that the customer is not limited to using Dachser transport networks, but also commissions Dachser to take care of warehousing, picking, packaging, display building or other individual services.For the customers, the key factor is that the contract logistics provider can integrate their specific requirements into a standardised physical and IT network. It is very costeffective. Moreover, it ensures freight capacity utilisation is higher, which in turn keeps overall process costs lower than they would be if the companies handled all these tasks themselves.
The final advantage of contract logistics services that form an integral part of logistics providers’ freight network, is security. Such systems offer direct access. Capacities can be guaranteed, even when there is a bottleneck in the market. Such one-stop shopping provides a global cost…
arrow_forward
Roger Ginde is developing a program in supply chain management certification for managers. Ginde has listed a number of activities that must be completed before a training program of this nature
could be conducted. The activities, immediate predecessors, and times appear in the accompanying table:
Immediate Predecessor(s)
Activity
A
B
C
D
E
F
G
This exercise contains only parts b, c, and d.
b) The critical activities for the leadership training program development project are A-E-G
c) The project length for the leadership training program development project = 22 days.
d) Slack time for each of the activities is:
B
A, D
C
E, F
Activity
A
B
Slack Time
0
Time (days)
10
6
3
2
4
8
arrow_forward
Draw project network
arrow_forward
Describe Low Priority Objectives.
arrow_forward
SEE MORE QUESTIONS
Recommended textbooks for you
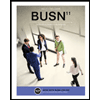
BUSN 11 Introduction to Business Student Edition
Business
ISBN:9781337407137
Author:Kelly
Publisher:Cengage Learning
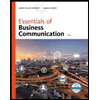
Essentials of Business Communication (MindTap Cou...
Business
ISBN:9781337386494
Author:Mary Ellen Guffey, Dana Loewy
Publisher:Cengage Learning
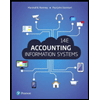
Accounting Information Systems (14th Edition)
Business
ISBN:9780134474021
Author:Marshall B. Romney, Paul J. Steinbart
Publisher:PEARSON
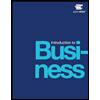
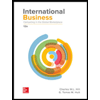
International Business: Competing in the Global M...
Business
ISBN:9781259929441
Author:Charles W. L. Hill Dr, G. Tomas M. Hult
Publisher:McGraw-Hill Education
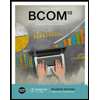
Related Questions
- Scenario Capstone project Goal Statement: Our goal is to improve the overall mental health status of veterans of the Canadian Armed Forces and RCMP by up to 80% for those struggling with mental health challenges by facilitating real-time accessibility to a peer support platform utilizing a mobile app to fill the gap that currently exists when veterans are awaiting appointments for psychological supports that are currently funded by Veterans Affairs of Canada. We aim to reduce the strain on the general health system due to the repeated appointments with a veteran's primary care practitioner to inquire about further mental health resources and to improve a veterans quality of life while they are adjusting to civilian life in between their federally funded psychological supports. Please answer in detail 1 communication strategy for the above project 2. Pilot or stakeholder feedback outcomes 3. Recommendation for next stepsarrow_forwardScenario 8.3- Mousetraps A company faces the aggregate planning problem shown in the table below. Cost of regular production is $15 per unit, the cost of producing the same unit on overtime is $22.50, the cost subcontracting is $27 per unit, and the cost of carrying a unit in inventory from one month to the next is $10. Forecast Beginning Inventory Regular Time Overtime Subcontracting Ending Inventory The labor contract at the plant prohibits both overtime and subcontracting output to exceed 250 units in any five-month window. The plant capacity is 20 units per day produced using two shifts and the plant runs seven days a week. By policy, management wants to avoid stockouts. August Which month has a positive ending inventory for the optimal aggregate plan for Scenario 8.3? September July 800 140 O October August September October November 650 450 550 900 Novemberarrow_forwardAnswer Activity 3arrow_forward
- DEFINE Critical path analysisarrow_forwardFor the following schedule, draw the arrow and node diagram. Activity Duration IPA A----3---- ABCDEFGHISKENN с H----------5------ --4- -3--- L- -6---- -3------ -9------ -1- M N----- 3636 B A -9 --A B C, D C,D E F, G, H F, G, H I J, K - GOD BLESS ---arrow_forwardDescribe the role of supply chain management in project management and its significance in guaranteeing the successful completion of the project.arrow_forward
- Preceding Activity Crashed Cost per week $600 $700 $400 Activity Normal Completion Time (week) Crashed Completion time (week) A 7 5 B 12 10 A 8 2 $800 $300 $500 E C, D 5 4 F E 9 8 D. F 10 10 i. Draw the network diagram linking all the activities in a way that it shows if there exist any preceding activity/activities before starting each of the mentioned activities in the above table, ii. Showing the earliest start time, the earliest finish time, the latest start time and the latest finish time of each of the activities in the project determine the completion time of the project and the critical path. ii. Find the slack time (delay time) of each of the activities, the critical and the non-critical activities. Find the minimum possible completion time of the project by considering the crashed completion times and the minimal total cost of that crashing the project. iv. Need proper handwritten answers. Thank you!arrow_forwardThe Custom Bike Company has set up a weighted scoring matrix for evaluation of potential projects. Following are five projects under consideration. Criteria Strong sponsor Supports business strategy Urgency 10% of sales from new products Competition Fill market gap Weight 2 4 2 5 1 2 Project 1 6 8 9 5 4 0 Project 2 9 8 4 2 7 10 Project 3 3 2 3 9 4 8 Project 4 9 6 6 1 4 0 Project 5 6 0 7 4 1 0 Using the scoring matrix above, what score would you give to each project?arrow_forwardCase stady: Global Village: A tourist attraction Global Village is the region’s leading family outdoor cultural and entertainment destination and one of Dubai’s most exciting and unique annual tourism and cultural destination. The theme park offers a vast selection of multicultural entertainment and retail options. Launched in 1997, Global Village made its entrance on the Creek Side opposite Dubai Municipality, and later moved to Oud Metha and then Dubai Festival City, until it found a permanent home on the outskirts of Dubai Land in 2005. Over the past 17 years, Global Village has been providing cultural entertainment along with an international shopping experience to millions of visitors. From hosting 18 country pavilions in 1997, Global Village has expanded over the years to now include over 37 pavilions, with added entertainment and culinary attractions with every season. Apart from this breathtaking live performances, mouth-watering cuisine, authentic handicrafts and merchandise…arrow_forward
- Describe Short Term High Priority Objectives.arrow_forwardCarlos Cavalas, the manager of Echo Products’ Brazilian Division, is trying to set the production schedule for the last quarter of the year. The Brazilian Division had planned to sell 70,070 units during the year, but by September 30 only the following activity had been reported: Units Inventory, January 1 0 Production 71,100 Sales 63,700 Inventory, September 30 7,400 The division can rent warehouse space to store up to 30,500 units. The minimum inventory level that the division should carry is 2,800 units. Mr. Cavalas is aware that production must be at least 4,440 units per quarter in order to retain a nucleus of key employees. Maximum production capacity is 44,200 units per quarter. Demand has been soft, and the sales forecast for the last quarter is only 19,500 units. Due to the nature of the division’s operations, fixed manufacturing overhead is a major element of product cost. Required: 1a. Assume that the division is using variable costing. How many…arrow_forwardRoger Ginde is developing a program in supply chain management certification for managers. Ginde has listed a number of activities that must be completed before a training program of this nature could be conducted. The activities, immediate predecessors, and times appear in the accompanying table: Immediate Predecessor(s) Activity ABCDEFG This exercise contains only parts b, c, and d. b) The critical activities for the leadership training program development project are B A, D C E, F Time (days) 4 5 3 10 4 6 10arrow_forward
arrow_back_ios
SEE MORE QUESTIONS
arrow_forward_ios
Recommended textbooks for you
- BUSN 11 Introduction to Business Student EditionBusinessISBN:9781337407137Author:KellyPublisher:Cengage LearningEssentials of Business Communication (MindTap Cou...BusinessISBN:9781337386494Author:Mary Ellen Guffey, Dana LoewyPublisher:Cengage LearningAccounting Information Systems (14th Edition)BusinessISBN:9780134474021Author:Marshall B. Romney, Paul J. SteinbartPublisher:PEARSON
- International Business: Competing in the Global M...BusinessISBN:9781259929441Author:Charles W. L. Hill Dr, G. Tomas M. HultPublisher:McGraw-Hill Education
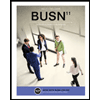
BUSN 11 Introduction to Business Student Edition
Business
ISBN:9781337407137
Author:Kelly
Publisher:Cengage Learning
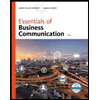
Essentials of Business Communication (MindTap Cou...
Business
ISBN:9781337386494
Author:Mary Ellen Guffey, Dana Loewy
Publisher:Cengage Learning
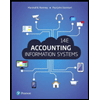
Accounting Information Systems (14th Edition)
Business
ISBN:9780134474021
Author:Marshall B. Romney, Paul J. Steinbart
Publisher:PEARSON
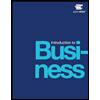
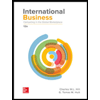
International Business: Competing in the Global M...
Business
ISBN:9781259929441
Author:Charles W. L. Hill Dr, G. Tomas M. Hult
Publisher:McGraw-Hill Education
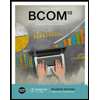